Systems Engineering
The mechanical and electrotechnological systems used in our homes and industry have a significant effect on society and the environment. The aim of VCE Systems Engineering is to apply innovative systems thinking and problem-solving skills to understand how technologies can transform people’s lives.
In the study, students design, construct and assemble an operational, integrated and controlled system using both mechanical components, such as gearboxes, pulleys, drivers and motors, and electrotechnological components, such as circuitry and sensors. Applying technological, mathematical and scientific principles, the students design a solution for a system-based problem, need, opportunity or situation. They plan and record production activities, then testing and evaluation is undertaken. The systems selected for exhibition were completed as School-assessed Tasks, addressing Outcome 1 of Units 3 and 4.
Moses Huf-Tirfe
Footscray High School, Footscray
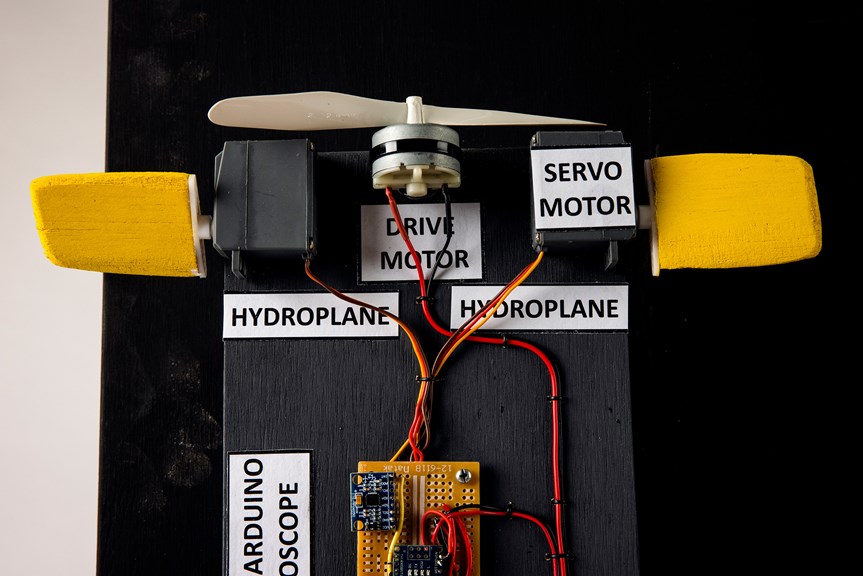
The Autonomous Underwater Vehicle (AUV)
MPU6050 Gyroscope, Arduino Nano, NPN MOSFET, 5V solar panel, servomotors, 12V submersible impeller pump, DC motor, 12V battery, protoboard, PVC tubing, ABS plastic for 3D printing, acrylic plastic for laser cutting, plywood, acrylic and enamel paints, hot glue, super glue, solder, hook up wires
The function of this system is to autonomously travel to predetermined locations using GPS technology to collect data on aquatic environmental conditions. The AUV can automatically stabilise itself along the X-axis by detecting the roll instability, then actuating the hydroplanes to create a counter roll. It can also dive and surface by filling and purging the contents of the external ballast tanks. The solar panel charges the battery when the AUV has surfaced.
Scott Keane
Padua College, Mornington
Automatic Waterway Cleaning Unit
PLA 3D printer filament, 3mm transparent blue acrylic, Arduino Mega, Arduino compatible 5V Laser diode, LDR, 1KOhm resistor, Nema 17 Stepper Motor, L298N Stepper motor driver, 3A fuse and holder, 6V SLA battery, Switch, 8mm inner diameter bearings, 8mm diameter smooth linear rods
I have created an aquatic waste-removal system designed to collect, measure and store litter that is present in local waterways, to decrease the impact of human activity on the aquatic ecosystems. My completed subsystem detects oncoming waste through a light-based sensor and temporarily activates a conveyor belt to collect it. The partially submerged conveyor belt retrieves large waste items, as well as pollutant particles from running water. The intention is for this waste to then be stored and prepared for appropriate disposal once a threshold is reached.
Haden Kneller
Bendigo Senior Secondary College, Bendigo
Wildlife Population Tracking Device
‘X AUTOHAUX’ Twin outlet windscreen washer pump, Samsung wired earphones, plywood, Nema 23 1.26Nm stepper motor, 2X Ultrasonic sensors, Turnigy 11.1V/2200mAh LiPo battery, LM 2596 DC-DC buck converter, LiPo low battery alarm, Stripboard (Veroboard), 25mm pulley, 3mm utility cord, 3mm vinyl clear tubing, XT60 Parallel splitter, Tower- Pro Micro servo, four-channel relay module, L298N stepper motor driver, NEMA 23 mounting bracket, 2X Ultraviolet LED, 110 ohm resistor, sprinkler PVC tubing, metal wire, plastic Tupperware, Arduino jumper cables
I have produced a wildlife tracking system that can rehabilitate, tag and capture photos of ‘at-risk’ animals autonomously in a nature setting. My system reliably dispenses food and water, tags the animal with a UV ink-water mixture, captures a photo with a UV flash, then releases the animal – all without human interaction.
Matthew Lewington
Hazel Glen College, Doreen
Robotic Dog
Wood, plastic, metal, motors, wires, Arduino, Raspberry Pi
My robotic dog was designed to prove that cheap and functional robotic dogs are possible to build using current technology. I intended for my system to, at a minimum, stand up and, at best, perform some basic walking. The robotic dog’s body was designed in CAD, then 3D-printed and laser cut. It utilises components from across the world, such as geared motors and L298n H-bridge drivers, to move its legs. It is powered by an Arduino MEGA and a Raspberry Pi Zero for serial communication.
Seetali Mack
Beaconhills College, Pakenham
Rural Solar Station
Solar panel, servo motors, light dependant resistors, ultrasonic sensors, rain sensor, washer pump
My project is an integrated solar station that aims to make farmers’ lives easier by having a fully automated water trough and electric gate. The pump is automatically filled based on a rain sensor while the gate automatically opens in response to an ultrasonic sensor. It also features a solar tracking system that moves a solar panel towards the sun.
This project could be made on a larger scale by incorporating the use of a camera and remote control for the gate. This would allow a farmer to view and control his cattle without having to travel great distances.
Hugh Mayer
Padua College, Mornington
Prototype Automatic Continuously Variable Bicycle Transmission
PLA printed plastic, 16mm outer diameter galvanised steel threaded rod, 6.3mm aluminium rod, 6mm x 52mm outer, 25mm inner sealed bearings, Arduino UNO, 28byj-48 stepper motor, Hall effect sensor, magnet, DRV8825 motor driver, 9V 500mAh non-rechargeable battery, 9V 1A wall plug with 2mm DC socket head bread board, jumper leads
This product is designed to provide an alternative gear-changing system to the conventional drivetrains used on common bicycles. As the user rides the transmission changes the output ratios autonomously in response to a sensory detection of a magnet on a rotating crank arm. As a result of this, the rider is always at the optimal pedalling cadence.
Miles Nathan
Kilvington Grammar School, Ormond
BRUCE
3D printer PLA, 3mm MDF wood, Arduino Uno, L298n motor shield, 9G servos, 12V DC motor, MPU6050 Gyroscope, HM10 Bluetooth module, LED weights, AA batteries, 0.5mm aluminium, 52n magnets
The BRUCE (Ball Rolling Under Centrical Energy) is a spherically shaped ball robot. It works by having a large counter weight move inside the ball. The ball rolls down to move the counterweight to the bottom, and so on. To turn, the counterweight moves to one side and the whole ball leans, therefore rolling on a smaller circumference circle and causing it to turn. In addition to this, the ball also has active gyroscopic stabilisation that corrects any unwanted movement in less than a second.
Alexander Stevensen
Christian College Geelong, Waurn Ponds
Racing Simulator
OMRON-E6B2-CWZ6C rotary encoder, M8 bolts, M5 bolts, M8 lock nuts, M5 lock nuts, H-bridge BTS7960, Arduino Leonardo, MOMO steering wheel, switches, springs, potentiometers (100k ohms), aluminium U extrusion (30mm x 30mm x 1000mm), aluminium U extrusion (40mm x 40mm x 1000mm), marine carpet, united MY6812 24V DC motor (100W), 24V 5A transformer, plywood
My project is a racing simulator that incorporates a sequential manual transmission, a steering wheel with force feedback and auto zeroing, an accelerator and a brake pedal. These parts are to be used simultaneously on a Windows 10 device whereby the entire system can be used in racing simulation video games to simulate real world driving.
Valentino Vargetto
Marcellin College
Vision Impairment Smart Cane
Arduino Nano V3.0 Board, DFRobot VL53L0X ToF laser range finder, FEETECH FS90R micro continuous rotation servo,18650 2600mAh Li-Ion rechargeable batteries, 18650 battery holders, SparkFun Li-ion Charger Plus, Pololu Adjustable 4-12V Step-Up Voltage Regulator U3V50ALV, SPDT sub-miniature toggle switch, 2 x 2.7 ohm 1 watt resistors, fibreglass tube, spray paint, Super Glue, bolts and nuts, wires, lead-free solder, black heat-shrink tubing
I designed and produced an electromechanical system that can assist people who are visually impaired communicating the distance of objects around the user. A sensor detects an object’s distance in front of the smart cane, which is then communicated to the user through the handle. The user’s thumb is tapped at high frequencies when an object is close and low frequencies when an object is far away.